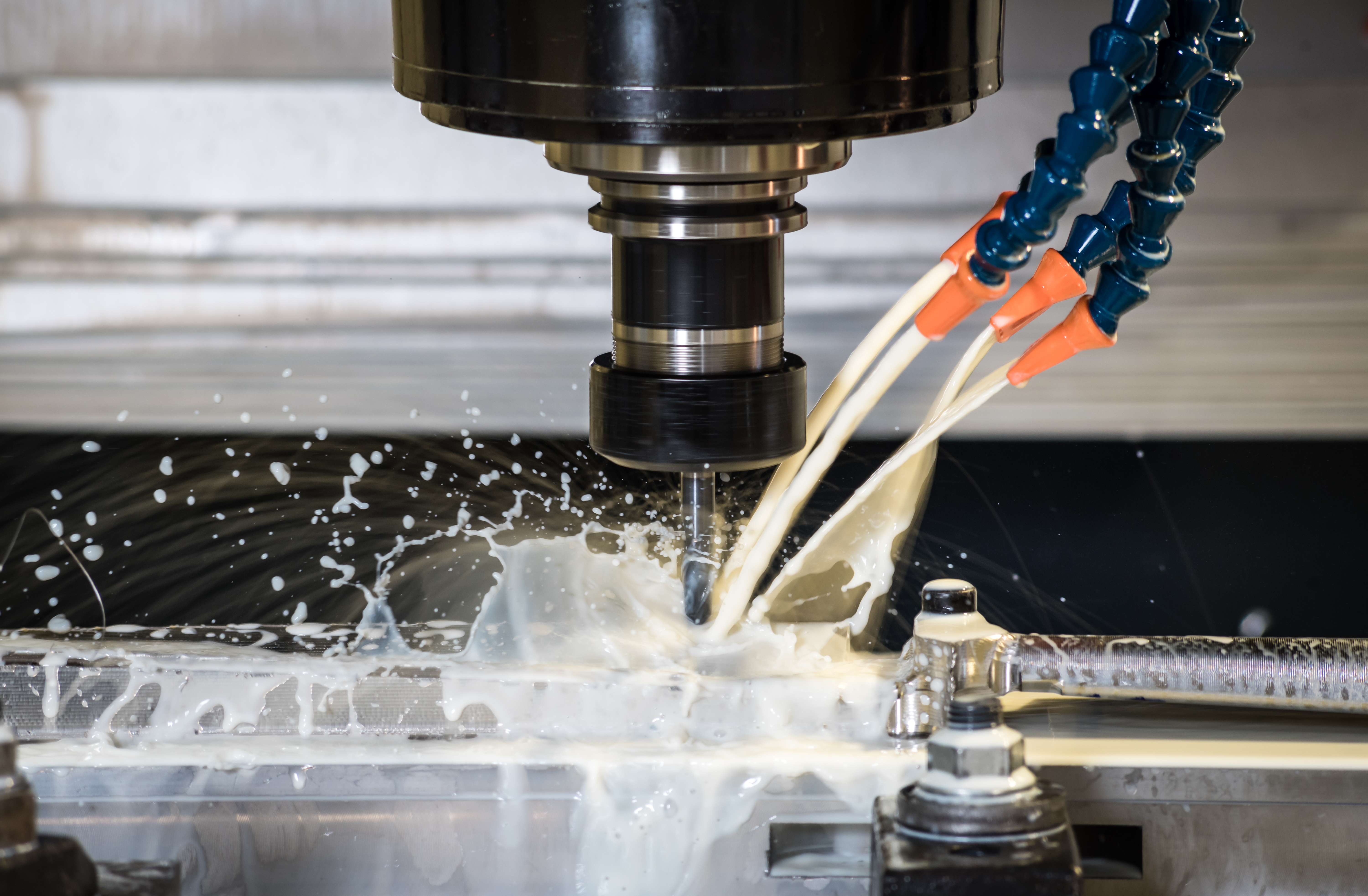
Finishing
Sandblasting:
Sandblasting is used to clean parts during repairs, both before and
after coating.
Ultrasonic
Cleaning:
Ultrasonic cleaning is used to clean parts received from turbine
stations. By using solvents and vibrations, it removes some of the surface and
internal contaminants and grease.
Chemical
Cleaning:
In the repair process, chemical stripping is used to remove the
previous coating (de-coating). Depending on the type of coating, a specific
solvent with controlled temperature is used.
Welding:
Welding processes such as TIG (Tungsten Inert Gas) and GTAW (Gas
Tungsten Arc Welding), as well as laser welding, are utilized.
Heat Treatment:
Heat treatment can be performed under argon, hydrogen, or a mixture
of both gases. This heat treatment can be carried out using our equipped and
calibrated furnaces, including:
• Solution heat treatment up to 1200°C
• Aging treatment
• Thermal coloring
Finishing
Sandblasting:
Sandblasting is used to clean parts during repairs, both before and
after coating.
Ultrasonic
Cleaning:
Ultrasonic cleaning is used to clean parts received from turbine
stations. By using solvents and vibrations, it removes some of the surface and
internal contaminants and grease.
Chemical
Cleaning:
In the repair process, chemical stripping is used to remove the
previous coating (de-coating). Depending on the type of coating, a specific
solvent with controlled temperature is used.
Welding:
Welding processes such as TIG (Tungsten Inert Gas) and GTAW (Gas
Tungsten Arc Welding), as well as laser welding, are utilized.
Heat Treatment:
Heat treatment can be performed under argon, hydrogen, or a mixture
of both gases. This heat treatment can be carried out using our equipped and
calibrated furnaces, including:
• Solution heat treatment up to 1200°C
• Aging treatment
• Thermal coloring